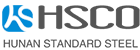
ERW Pipe Meaning: ERW pipe refers to "straight seam electric resistance welded pipe", involving Electric Resistance Welding, abbreviated as ERW. ERW pipes are made of steel strips or steel plates that are rolled and then welded, with the welds parallel to the pipes. The ERW welded pipe production line can produce high-frequency resistance longitudinal welded pipes, square pipes, rectangular pipes, steel sheet piles and other products.
ERW straight seam welded pipes are mainly divided into two forms: ERW AC welded steel pipes and ERW DC welded steel pipes. ERW straight seam welded pipes are divided into low frequency welding, medium frequency welding, super medium frequency welding and high frequency welding according to different frequencies. High-frequency welding (HFW) is mainly used for the production of thin-walled steel pipes or ordinary-walled steel pipes. High-frequency welding is divided into contact welding and induction welding.
Electric resistance welding is a kind of pressure welding, in which the edge of the weld is heated to the welding temperature and pressure welds the welded pipe of the composite pipe. It is divided into low frequency and high frequency. Unlike ordinary welded pipe welding process, the weld is formed by melting the base material of the steel strip body, and its mechanical strength is better than that of ordinary welded pipe. The welding methods of erw pipes and submerged arc welded pipes are significantly different. The pressure welding method without filler metal is adopted. There are no other components filled in the weld. The skin effect and proximity effect of the high-frequency current make the edge of the plate instantaneously heated. When the welding temperature is reached, the welding seam of the forging structure is formed by the extrusion roller. High-quality steel pipes require on-line or off-line heat treatment of welds to refine the weld zone structure. The welds of high-quality erw welded pipes can reach the same toughness level as the base metal, which cannot be achieved by submerged arc welding.
The production process of ERW welded pipe generally includes the following steps:
1. Raw material preparation: Select appropriate steel strip coils and check the quality, size and chemical composition of the steel strip.
2. Steel strip uncoiling: Unroll the rolled steel strip.
3. Steel strip leveling: The steel strip is straightened and flattened by a leveling machine to eliminate the bending and wavy shape of the steel strip.
4. Cut the ends neatly: Cut both ends of the steel strip neatly to ensure alignment during welding.
5. Steel strip forming: The steel strip is gradually bent into a tube shape through a forming machine.
6. High-frequency resistance welding: The resistance heat generated by high-frequency current passing through the contact point is used to instantly heat the edge of the steel strip to the welding temperature and pressurize it to achieve welding.
7. Removing internal and external burrs from the weld seam: Use special devices to remove burrs from the internal and external surfaces of the weld seam to ensure the quality of the weld seam and the smoothness of the inner wall of the steel pipe.
8. Weld heat treatment: Appropriate heat treatment of the weld to improve the structure and performance of the weld.
9. Sizing and shaping: The diameter and shape of the steel pipe are accurately adjusted and shaped through the sizing machine.
10. Non-destructive testing: Use non-destructive testing methods such as ultrasonic and eddy current to check the quality of steel pipe welds and pipe bodies.
11. Cutting and finished product inspection: Cut the steel pipe according to the specified length, and conduct final quality inspection, including inspection of appearance, size, performance, etc.
Electric resistance welding has the characteristics of high production efficiency, low cost, material saving, and easy automation. Therefore, it is widely used in aviation, aerospace, energy, electronics, automotive, light industry and other industrial sectors. It is one of the important welding processes. One. It is especially used to transport oil, natural gas and other vapor and liquid objects, which can meet various requirements of high and low pressure. Currently, it occupies a pivotal position in the field of transportation pipes in the world.
Read more: Classification and application of welded steel pipe
Related information