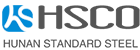
Large caliber straight double submerged arc welding pipe joints uses the most advanced domenstic hydraulic bending process, the bending machine is duplex structure, maximum lenght up to 16mm, the pressure of 1600 tons, single-equipment weighing about more than 400 tons, machinable diameter of 325-3250 mm and the wall thickness 6-30 mm of ordinary and special steel pipe.
Plate Edge Milling Machine
The milling machine mills the two sides of the plate to exacting standards in order to meet width , edging and groove shape specifications.
Specification:
Nominal pressure of squeeze head: 2x2000 ton
Movement for each squeeze: 2200mm(max)
Thickness range of steel plate: 6-50mm
Edge Crimping Machine
The crimping machine crimps the edges of the plate to form the required curvature.
Specification:
Milling units: 4 sets
Nominal diameter of cutter head : cD800mm
Groove types: X type, I type and K type
Tack Welding Machine
The two edges of the open seam pipe are brought together by the tack welding machine. then welded by the tack welder using a metal active - gas arc welding("MAG" )process.
Specification:
Adjustment for roller beam:
mechanical adjustment
Roller beams: 9
Welding method: C02/ArMAGwelding
Welding tracking system : laser tracking
Forming Machine
Utilizes the "JCO" process to bend and form the crimped steel plate into a steel pipe.
Specification:
Nominal pressure: 5200 ton
Main cylinders: 6
Diameter of formed pipe:508mm ≤D≤1422mm
Interior Welding Machine
The interior longitudinal seam of the pipe is welded from the inside by fixing 4 welding heads while moving pipe and using submerged-arc welding process.
Specification :
Multiple wires: 4
Welding current: Direct
Current 400-2000A
Alternating Current 300-1200A
Welding head tracking system :mechanical tracking
Exterior Welding Machine
The exterior longitudinal seam of the pipe is welded from the inside by fixing 4 welding heads while moving pipe and using submerged-arc welding process.
Specification:
Multiple wire s: 5
Welding current: Direct
Current 400-2000A
Alternating Current 300- 1200A
Welding head tracking system: mechanical tracking
End facing Machine
The machine levels the pipe end with rotating cutter heads to ensure that required groove and edge specifications are met.
Technical specification :
Pipe end groove : flat end or beveled end (subject to the specification)
Wall thickness range : 6-50mm
Technical specification :
Diameter range: 518≤D≤1422mm
Hydrostatic Tester
Using end face sealing technology eliminates blind zones during hydrostatic testing. The tester is also equipped with automatic recording and storing functions.
Specification:
Maximum load-bearing capacity: 4000 ton
Testing pressure : 3-50 Mpa
Seal form: end pressure : 25Mpa
radial pressure ~ 25Mpa
Expanding Machine
The pipe is subjected to full-length expansion to increase the precision of the pipe dimensions and to improve the internal stress distribution.
Specification:
Nominal tensile force: 1600 ton
Expanding frequency: 15-18 seconds for each time
Expanding ratio: 0.3%-1.5%
Automated Ultrasonic Testing Equipment
The superiority of phased arrayultra sonic technology:
(1 )Adopting electron control method for fast linear scanning or sector scanning without moving probe or moving less. thus greatlyim prove detection efficiency .
(2)Controlting the sound beam by setting detection angles, its good sound beam reachability can enhances reliability and accuracy of detection.
(3) Dynamic control the deflection and focus of sound beam realizes the detection of pipes with different wall thickness without replacing probes.
Technical specification:
Testing method: pulse echo method
Detection channels: ~ 24
Probe: phased array probe