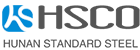
Spiral steel pipe, also known as spiral welded pipe, is made by rolling low-carbon structural steel or low-alloy structural steel strip into a tube blank at a certain spiral angle (called forming angle), and then welding the tube seams. It can produce large-diameter steel pipes with narrower strip steel.
Features:
The production process of straight seam welded pipe (ERW/LSAW) is simple, with high production efficiency, low cost and rapid development. The strength of spiral welded pipe is generally higher than that of straight seam welded pipe. It can produce welded pipes with larger diameters with narrower billets, and can also produce welded pipes with different diameters with billets of the same width. However, compared with straight seam pipes of the same length, the weld length increases by 30~100%, and the production speed is lower. Therefore, most smaller diameter welded pipes use straight seam welding, while large diameter welded pipes mostly use spiral welding.
Standard & Class
Classfication |
Standard |
Main Products |
Steel Pipe for Fluid Service |
GB/T 14291 |
Welded pipe for mine fluid sevice |
GB/T 3091 |
Welded pipe for low pressure fluid service |
|
SY/T 5037 |
Spirally submerged arc welded steel pipe for pipelines for low pressure fluid service |
|
ASTM A53 |
Black and hot-hipped galvanized welded and seamless steel pipe |
|
BS EN10217-2 |
Welded steel tybes for pressure purposes - delivery technical conditions - part2: Electric welded non- alloy and alloy steel tubes with specified elevated temperature properties |
|
BS EN10217-5 |
Welded steel tybes for pressure purposes - delivery technical conditions - part5: submerged arc welded non-alloy and alloy steel tubes with specified elevated temperature properties |
|
Steel Pipe for Ordinary Structure |
GB/T 13793 |
Longitudinally electric resistance welded steel pipe |
SY/T 5040 |
Spirally submerged arc welded steel pipe piles |
|
ASTM A252 |
Welded and seamless steel pipe piles |
|
BS EN10219-1 |
Cold formed welded structural hollow sections of non-alloy and fine grain steels - part1: Technical delivert conditions |
|
BS EN10219-2 |
Cold formed welded structural hollow sections of non-alloy and fine grain steels - part2: tolerances dimmsions and sectional properties |
|
Line Pipe |
GB/T 9711.1 |
Steel pipe for pipeline transportation system of petroleum and natural gas industries(Class A steel pipe) |
GB/T 9711.2 |
Steel pipe for pipeline transportation system of petroleum and natural gas industries(Class B steel pipe) |
|
API 5L PSL1/2 |
Line pipe |
|
Casing |
API 5CT/ ISO 11960 PSL1 |
Steel pipe for use as casing or tubing for wells of petroleum and natural gas industries |
Chemical Analysis and Mechanical Properties
Standard |
Grade |
Chemical Composition(max)% |
Mechanical Properties(min) |
|||||
C |
Si |
Mn |
P |
S |
Tensile Strength(Mpa) |
Yield Strength(Mpa) |
||
API 5CT |
h40 |
- | - | - | - |
0.030 |
417 |
417 |
J55 |
- | - | - | - |
0.030 |
517 |
517 |
|
K55 |
- | - | - | - |
0.030 |
655 |
655 |
|
API 5L PSL1 |
A |
0.22 |
- |
0.90 |
0.030 |
0.030 |
335 |
335 |
B |
0.26 |
- |
1.20 |
0.030 |
0.030 |
415 |
415 |
|
X42 |
0.26 |
- |
1.30 |
0.030 |
0.030 |
415 |
415 |
|
X46 |
0.26 |
- |
1.40 |
0.030 |
0.030 |
435 |
435 |
|
X52 |
0.26 |
- |
1.40 |
0.030 |
0.030 |
460 |
460 |
|
X56 |
0.26 |
- |
1.40 |
0.030 |
0.030 |
490 |
490 |
|
X60 |
0.26 |
- |
1.40 |
0.030 |
0.030 |
520 |
520 |
|
X65 |
0.26 |
- |
1.45 |
0.030 |
0.030 |
535 |
535 |
|
X70 |
0.26 |
- |
1.65 |
0.030 |
0.030 |
570 |
570 |
|
API 5L PSL2 |
B |
0.22 |
0.45 |
1.20 |
0.025 |
0.015 |
415 |
415 |
X42 |
0.22 |
0.45 |
1.30 |
0.025 |
0.015 |
415 |
415 |
|
X46 |
0.22 |
0.45 |
1.40 |
0.025 |
0.015 |
435 |
435 |
|
X52 |
0.22 |
0.45 |
1.40 |
0.025 |
0.015 |
460 |
460 |
|
X56 |
0.22 |
0.45 |
1.40 |
0.025 |
0.015 |
490 |
490 |
|
X60 |
0.12 |
0.45 |
1.60 |
0.025 |
0.015 |
520 |
520 |
|
X65 |
0.12 |
0.45 |
1.60 |
0.025 |
0.015 |
535 |
535 |
|
X70 |
0.12 |
0.45 |
1.70 |
0.025 |
0.015 |
570 |
570 |
|
X80 |
0.12 |
0.45 |
1.85 |
0.025 |
0.015 |
625 |
625 |
|
GB/T 9711.1 |
L210 |
- | - |
0.90 |
0.030 |
0.030 |
335 |
335 |
L245 |
- | - |
1.15 |
0.030 |
0.030 |
415 |
415 |
|
L290 |
- | - |
1.25 |
0.030 |
0.030 |
415 |
415 |
|
L320 |
- | - |
1.25 |
0.030 |
0.030 |
435 |
435 |
|
L360 |
- | - |
1.25 |
0.030 |
0.030 |
460 |
460 |
|
L390 |
- | - |
1.35 |
0.030 |
0.030 |
490 |
490 |
|
L415 |
0.26 |
- |
1.35 |
0.030 |
0.030 |
520 |
520 |
|
L450 |
0.26 |
- |
1.40 |
0.030 |
0.030 |
535 |
535 |
|
L485 |
0.23 |
- |
1.60 |
0.030 |
0.030 |
570 |
570 |
|
GB/T3091/ SY/T503 |
Q195 |
0.12 |
0.30 |
0.50 |
0.035 |
0.040 |
315 |
315 |
Q215B |
0.15 |
0.35 |
1.20 |
0.045 |
0.045 |
335 |
335 |
|
Q235B |
0.20 |
0.35 |
1.40 |
0.045 |
0.045 |
370 |
370 |
|
Q345B |
0.20 |
0.50 |
1.70 |
0.035 |
0.035 |
470 |
470 |
|
ASTM A53 |
A |
0.25 |
0.10 |
0.95 |
0.050 |
0.045 |
330 |
330 |
B |
0.30 |
0.10 |
1.20 |
0.050 |
0.045 |
415 |
415 |
|
ASTM A252 |
1 | - | - | - |
0.050 |
- |
345 |
345 |
2 | - | - | - |
0.050 |
- |
414 |
414 |
|
3 | - | - | - |
0.050 |
- |
455 |
455 |
|
EN10217-1 |
P195TR1 |
0.13 |
0.35 |
0.70 |
0.025 |
0.020 |
320 |
320 |
P195TR2 |
0.13 |
0.35 |
0.70 |
0.025 |
0.020 |
320 |
320 |
|
P235TR1 |
0.16 |
0.35 |
1.20 |
0.025 |
0.020 |
360 |
360 |
|
P235TR2 |
0.16 |
0.35 |
1.20 |
0.025 |
0.020 |
360 |
360 |
|
P265TR1 |
0.20 |
0.40 |
1.40 |
0.025 |
0.020 |
410 |
410 |
|
P265TR2 |
0.20 |
0.40 |
1.40 |
0.025 |
0.020 |
410 |
410 |
|
EN10217-2 |
P195GH |
0.13 |
0.35 |
0.70 |
0.025 |
0.020 |
320 |
320 |
P235GH |
0.16 |
0.35 |
1.20 |
0.025 |
0.020 |
360 |
360 |
|
P265GH |
0.20 |
0.40 |
1.40 |
0.025 |
0.020 |
410 |
410 |
|
EN10217-5 |
P235GH |
0.16 |
0.35 |
1.20 |
0.025 |
0.020 |
360 |
360 |
P265GH |
0.20 |
0.40 |
1.40 |
0.025 |
0.020 |
410 |
410 |
|
EN10219-1 |
S235JRH |
0.17 |
- |
1.40 |
0.040 |
0.040 |
360 |
360 |
S275JOH |
0.20 |
- |
1.50 |
0.035 |
0.035 |
410 |
410 |
|
S275J2H |
0.20 |
- |
1.50 |
0.030 |
0.030 |
410 |
410 |
|
S355JOH |
0.22 |
0.55 |
1.60 |
0.035 |
0.035 |
470 |
470 |
|
S355J2H |
0.22 |
0.55 |
1.60 |
0.030 |
0.030 |
470 |
470 |
|
S355K2H |
0.22 |
0.55 |
1.60 |
0.030 |
0.030 |
470 |
470 |
Tolerance of Outside Diameter and Wall Thickness
Standard |
Tolerance of Pipe Body |
Tolerance of Pipe End |
Tolerance of Wall Thickness |
|||
Out Diameter |
Tolerance |
Out Diameter |
Tolerance |
|||
GB/T3091 |
OD≤48.3mm |
≤±0.5 |
OD≤48.3mm |
- |
≤±10% |
|
48.3 |
≤±1.0% |
48.3 |
- | |||
273.1 |
≤±0.75% |
273.1 |
-0.8~+2.4 |
|||
OD>508mm |
≤±1.0% |
OD>508mm |
-0.8~+3.2 |
|||
GB/T9711.1 |
OD≤48.3mm |
-0.79~+0.41 |
- | - |
OD≤73 |
-12.5%~+20% |
60.3 |
≤±0.75% |
OD≤273.1mm |
-0.4~+1.59 |
88.9≤OD≤457 |
-12.5%~+15% |
|
508 |
≤±1.0% |
OD≥323.9 |
-0.79~+2.38 |
OD≥508 |
-10.0%~+17.5% |
|
OD>941mm |
≤±1.0% |
- | - |
- |
- | |
GB/T9711.2 |
60 |
±0.75%D~±3mm |
60 |
±0.5%D~±1.6mm |
4mm |
±12.5%T~±15.0%T |
610 |
±0.5%D~±4mm |
610 |
±0.5%D~±1.6mm |
WT≥25mm |
-3.00mm~+3.75mm |
|
OD>1430mm |
- |
OD>1430mm |
- | - |
-10.0%~+17.5% |
|
SY/T5037 |
OD<508mm |
≤±0.75% |
OD<508mm |
≤±0.75% |
OD<508mm |
≤±12.5% |
OD≥508mm |
≤±1.00% |
OD≥508mm |
≤±0.50% |
OD≥508mm |
≤±10.0% |
|
API 5L PSL1/PSL2 |
OD<60.3 |
-0.8mm~+0.4mm |
OD≤168.3 |
-0.4mm~+1.6mm |
WT≤5.0 |
≤±0.5 |
60.3≤OD≤168.3 |
≤±0.75% |
168.3 |
≤±1.6mm |
5.0 |
≤±0.1T |
|
168.3 |
≤±0.75% |
610 |
≤±1.6mm |
T≥15.0 |
≤±1.5 |
|
610 |
≤±4.0mm |
OD>1422 |
- |
- | - | |
OD>1422 |
- |
- |
- |
- | - | |
API 5CT |
OD<114.3 |
≤±0.79mm |
OD<114.3 |
≤±0.79mm |
≤-12.5% |
|
OD≥114.3 |
-0.5%~1.0% |
OD≥114.3 |
-0.5%~1.0% |
≤-12.5% |
||
ASTM A53 |
≤±1.0% |
≤±1.0% |
≤-12.5% |
|||
ASTM A252 |
≤±1.0% |
≤±1.0% |
≤-12.5% |
Manufacturing process of SSAW steel pipe:
(1) Raw materials are strip steel coil, welding wire and flux. They must undergo strict physical and chemical inspection before being put into use.
(2) The head and tail of the strip steel are butt-jointed by single-wire or double-wire submerged arc welding. After being rolled into a steel pipe, automatic submerged arc welding is used for repair welding.
(3) Before forming, the strip steel is leveled, trimmed, planed, surface cleaned, conveyed and pre-bent.
(4) An electric contact pressure gauge is used to control the pressure of the oil cylinder on both sides of the conveyor to ensure the smooth conveying of the strip steel.
(5) Externally controlled or internally controlled roller forming is adopted.
(6) A weld gap control device is used to ensure that the weld gap meets the welding requirements. The pipe diameter, misalignment and weld gap are strictly controlled.
(7) Both internal and external welding are performed by single-wire or double-wire submerged arc welding using an American Lincoln electric welder to obtain stable welding specifications.
(8) All welds are inspected by online continuous ultrasonic automatic flaw detectors to ensure 100% non-destructive testing coverage of spiral welds. If there are defects, an automatic alarm will be sounded and a mark will be sprayed. The production workers can adjust the process parameters at any time to eliminate the defects in time.
(9) The steel pipes are cut into single pieces by an air plasma cutting machine.
(10) After cutting into single steel pipes, each batch of steel pipes must undergo a strict first inspection system to check the mechanical properties, chemical composition, fusion status, surface quality of the welds and non-destructive testing to ensure that the pipe making process is qualified before it can be officially put into production.
(11) The parts with continuous ultrasonic flaw detection marks on the welds are re-inspected by manual ultrasonic and X-ray. If there are defects, they are repaired and then subjected to non-destructive testing again until it is confirmed that the defects have been eliminated.
(12) The butt welds of the strip steel and the pipes where the T-joints intersect with the spiral welds are all inspected by X-ray television or film.
(13) Each steel pipe is subjected to a hydrostatic test, and the pressure is radially sealed. The test pressure and time are strictly controlled by a steel pipe water pressure microcomputer detection device. The test parameters are automatically printed and recorded.
(14) The pipe end is machined to accurately control the end face verticality, groove angle and blunt edge.
Out Diameter |
Wall Thickness (mm) |
|||||||||||||||||||
mm |
6 |
7 |
8 |
9 |
10 |
11 |
12 |
13 |
14 |
15 |
16 |
17 |
18 |
19 |
20 |
21 |
22 |
23 |
24 |
25 |
219.1 |
. |
. |
. |
. |
|
|
|
|
|
|
|
|
|
|
|
|
|
|
|
|
273 |
. |
. |
. |
. |
. |
|
|
|
|
|
|
|
|
|
|
|
|
|
|
|
323.9 |
. |
. |
. |
. |
. |
. |
. |
|
|
|
|
|
|
|
|
|
|
|
|
|
325 |
. |
. |
. |
. |
. |
. |
. |
|
|
|
|
|
|
|
|
|
|
|
|
|
355.6 |
. |
. |
. |
. |
. |
. |
. |
|
|
|
|
|
|
|
|
|
|
|
|
|
377 |
. |
. |
. |
. |
. |
. |
. |
. |
|
|
|
|
|
|
|
|
|
|
|
|
406.4 |
. |
. |
. |
. |
. |
. |
. |
|
|
|
|
|
|
|
|
|
|
|
|
|
426 |
. |
. |
. |
. |
. |
. |
. |
|
|
|
|
|
|
|
|
|
|
|
|
|
457 |
. |
. |
. |
. |
. |
. |
. |
|
|
|
|
|
|
|
|
|
|
|
|
|
478 |
. |
. |
. |
. |
. |
. |
. |
|
|
|
|
|
|
|
|
|
|
|
|
|
508 |
. |
. |
. |
. |
. |
. |
. |
|
. |
|
|
|
|
|
|
|
|
|
|
|
529 |
. |
. |
. |
. |
. |
. |
. |
|
. |
|
|
|
|
|
|
|
|
|
|
|
630 |
. |
. |
. |
. |
. |
. |
. |
|
. |
. |
|
|
|
|
|
|
|
|
|
|
711 |
. |
. |
. |
. |
. |
. |
. |
. |
. |
. |
. |
|
|
|
|
|
|
|
|
|
720 |
. |
. |
. |
. |
. |
. |
. |
. |
. |
. |
. |
|
|
|
|
|
|
|
|
|
813 |
|
. |
. |
. |
. |
. |
. |
. |
. |
. |
. |
. |
. |
|
|
|
|
|
|
|
820 |
|
. |
. |
. |
|
. |
. |
. |
. |
. |
. |
. |
. |
|
|
|
|
|
|
|
920 |
|
|
. |
. |
|
. |
. |
. |
. |
. |
. |
. |
. |
|
|
|
|
|
|
|
1020 |
|
|
. |
. |
. |
. |
. |
. |
. |
. |
. |
. |
. |
. |
. |
|
|
|
|
|
1220 |
|
|
. |
. |
. |
. |
. |
. |
. |
. |
. |
. |
. |
. |
. |
|
|
|
|
|
1420 |
|
|
|
. |
. |
. |
. |
. |
. |
. |
|
. |
. |
. |
. |
|
|
|
|
|
1620 |
|
|
|
|
. |
. |
. |
. |
. |
. |
. |
. |
. |
. |
. |
|
|
|
|
|
1820 |
|
|
|
|
|
. |
. |
. |
. |
. |
. |
. |
. |
. |
. |
|
|
|
|
|
2020 |
|
|
|
|
|
|
. |
. |
. |
. |
. |
. |
. |
. |
. |
|
|
|
|
|
2220 |
|
|
|
|
|
|
|
. |
. |
. |
. |
. |
. |
. |
. |
|
|
|
|
|
2500 |
|
|
|
|
|
|
|
. |
. |
. |
. |
. |
. |
. |
. |
. |
. |
. |
. |
. |
2540 |
|
|
|
|
|
|
|
|
. |
. |
. |
. |
. |
. |
. |
. |
. |
. |
. |
. |
3500 |
|
|
|
|
|
|
|
|
|
. |
. |
. |
. |
. |
. |
. |
. |
. |
. |
. |
Philippines ASTM A53 GR.B 457.2, 711.2*8 26523 meters |
Morocco API 5L ,GR.B 273,323,355*6.5mm 16500 meters |
Philippines ASTM A252 609.6*11mm 3600 MT |
Spain |
Serbia |
Guatemala API 5L, X52 PSL2 762*10 360 MT |
Lebanon A252, GR.2 609,812*7.5 19630 meters |
Spain ASTM A252/API 5L GR.B 46" 48" 62" STD 789 Nos |